What is deck seal
Deck water seal or often called Deck seal, is found on Oil tanker vessels to prevent the back flow of Hydrocarbon from the cargo tanks to Engine room.
As you must be knowing that inert Gas system is there on Tankers in order to reduce the Oxygen and Hydrocarbon level in the Cargo tanks.
Contents
-Purpose and working of deck seal
– Why bunker tanks are not inerted..??
So for that, there is Inert gas line(IG line) to supply Inert gas from Inert Gas plant(IG plant) to the cargo tanks.
Purpose and working of deck seal in Inert gas system
Let’s understand like this, if we are supplying Inert Gas(IG) from the IG plant to the cargo tanks and the pressure increases inside the cargo tanks.
Then due to high pressure inside the cargo tanks, there are very much chances that the Inert gas, which has now mixed with the hydrocarbons inside the cargo tanks might flow back to the Engine room.
And that might be catastrophic, as the hydrocarbon gases from the cargo tanks might cause explosion or fire inside the Engine room.
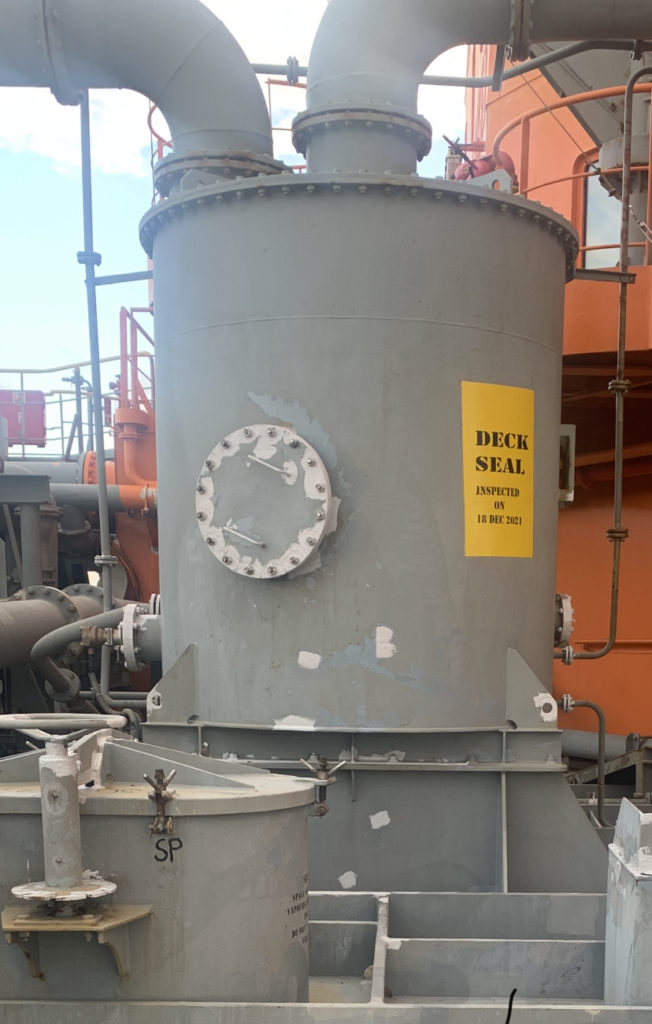
So in Order to control the back flow of Inert gas back to the Engine room, there is one Non return valve in the line. Which prevents the back flow of the IG to Engine room.
Because the non return valve is mechanical, so there are chances that it might leak and may cause the hydrocarbon gases to pass back to the Engine room.
Deck seal is built as a secondary barrier to prevent the back flow. Because in case the Non return valve doesn’t hold then Deck seal contains liquid seal to prevent the back flow.
Types of Deck seal
There are three types of deck seals found on board ships. The types are different based upon their structure and working.
Although the purpose is same, I.e. to stop the back flow of hydrocarbon gases to the Engine room. But the construction and design causes them to be named differently.
The working can be understood easily with the manual provided onboard. While the publication “Inert Gas” should be available onboard in the ship’s library.
Following are the types of deck seals you will come across onboard.
1. Wet type deck seal
As the name suggests, wet type of deck seal contains seal, made of water. Which is there to prevent the back flow of inert gas to the Engine room.
In wet type of deck seal, water is displaced by the gas thus creating a seal.
While the inert gas plant is in operation, the gas passes from the plant to the deck IG line via deck water seal. So while it is passing this way, it passes through the water.
The gas passing through the water causes bubbling of the gas. While on the other hand, if the tank pressure increases more than the pressure in the Inert gas line. Then it tries to run back to the Inert gas plant.
Thus the water seal acts as the barrier/ seal. Which prevents the back flow of the Inert gas which is now mixed up with hydrocarbon gases.
Disadvantage: The only disadvantage of the wet type deck seal is that it can carry water particles to the IG line.
These water particles can corrode the lines in long run. Thus a Demister pad is used normally to stop or reduce any carry over of water particles.
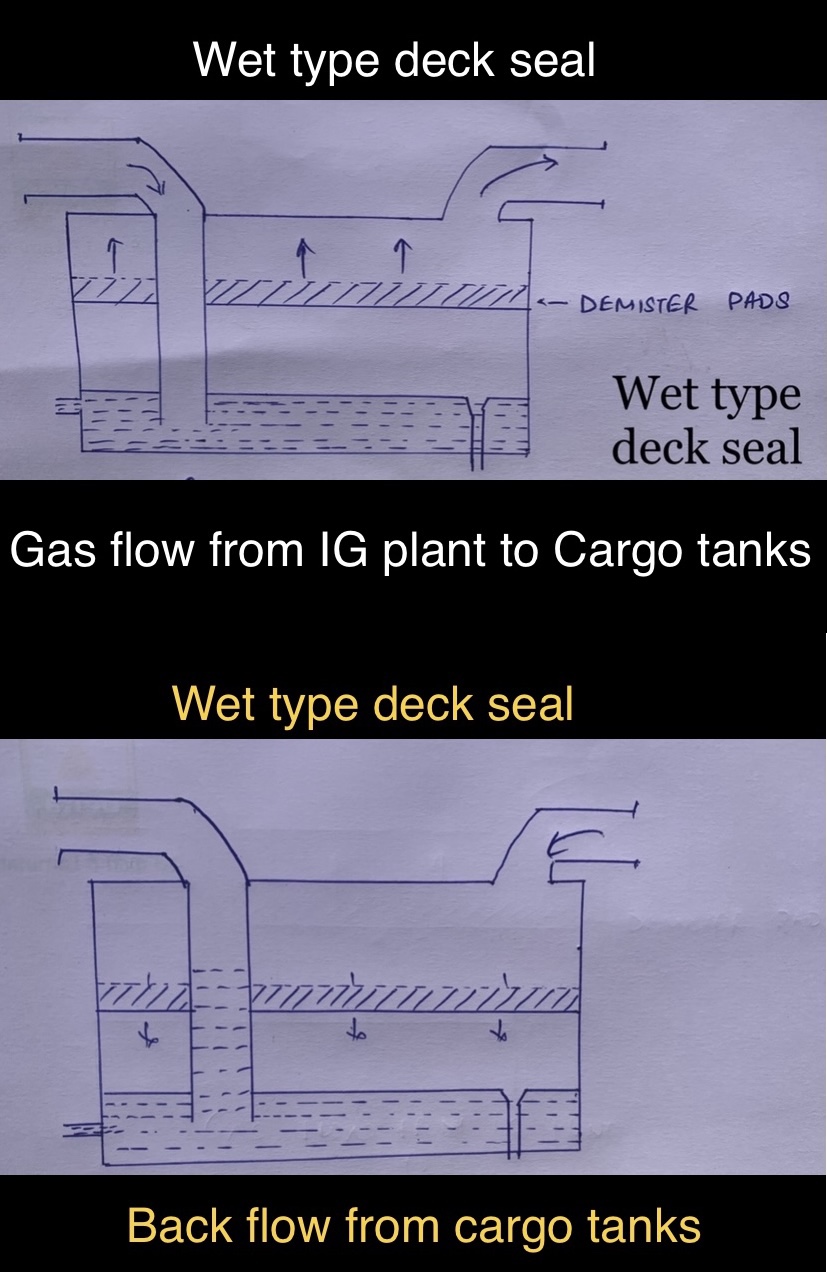
Wet type deck seal
Also read: Gyro compass- All you need to know
2. Semi dry deck seal:
Then there is semi-dry deck seal. In this type of deck seal, the Inert gas does not pass through the water like it passes in wet type deck seal.
In this kind of deck seal, there is a separate chamber or holding tank of water. The holding tank is connected to the main IG line via an educator.
So when the inert gas passes from the Venturi, it creates suction over there. The suction effect draws the sealing water to the holding tank. And because the water has not entered the main line, the possibility of water carriage to the cargo tanks reduces automatically.
While on the other hand, if the tank pressure increases the main line pressure, or the gas flow in the main line stops, the water from the holding tank flows rapidly to the U-bend in the main line.
The U-Bend in the main line is called loop seal, as it is shaped like a loop and acts as a seal to reduce the back flow.
So the loop seal thus prevents the back flow of the hydrocarbon vapour and the inert gas back to the Engine room.
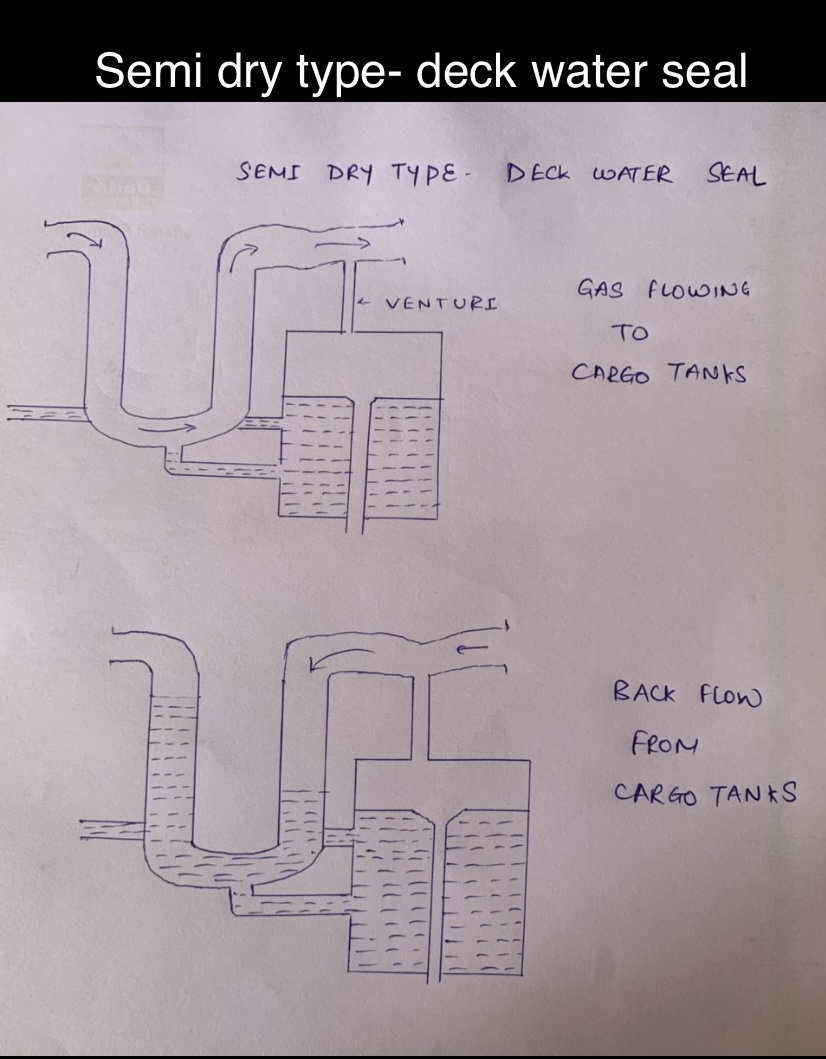
Semi dry type deck seal
3. Dry type deck seal:
The third and the most automated deck seal is dry type deck seal. There are two tanks inside the dry deck water seal.
The upper tank is called Drop tank or holding tank. While the lower tank is at the bottom of the deck seal, which is called sealing tank.
The drop tank has water filled in it at all times. And it supplies water to the lower tank.
So when the IG system is running and is in operation, the lower tank is empty and thus the water carriage to the cargo tanks reduces because of the dry inert gas flow.
And when the IG plant stops or the pressure inside the cargo tanks increases more than the main line pressure, Then the sensors are activated.
When they sense the levels inside the sealing and the drop tank, it starts the filling of the lower tank from the drop tank. And thus the water seal is created inside the deck seal thus restricting the back flow.
While on the other hand, when the sealing tank is overflowing, the overboard sensor valve is activated and the required level is maintained inside the sealing tank.
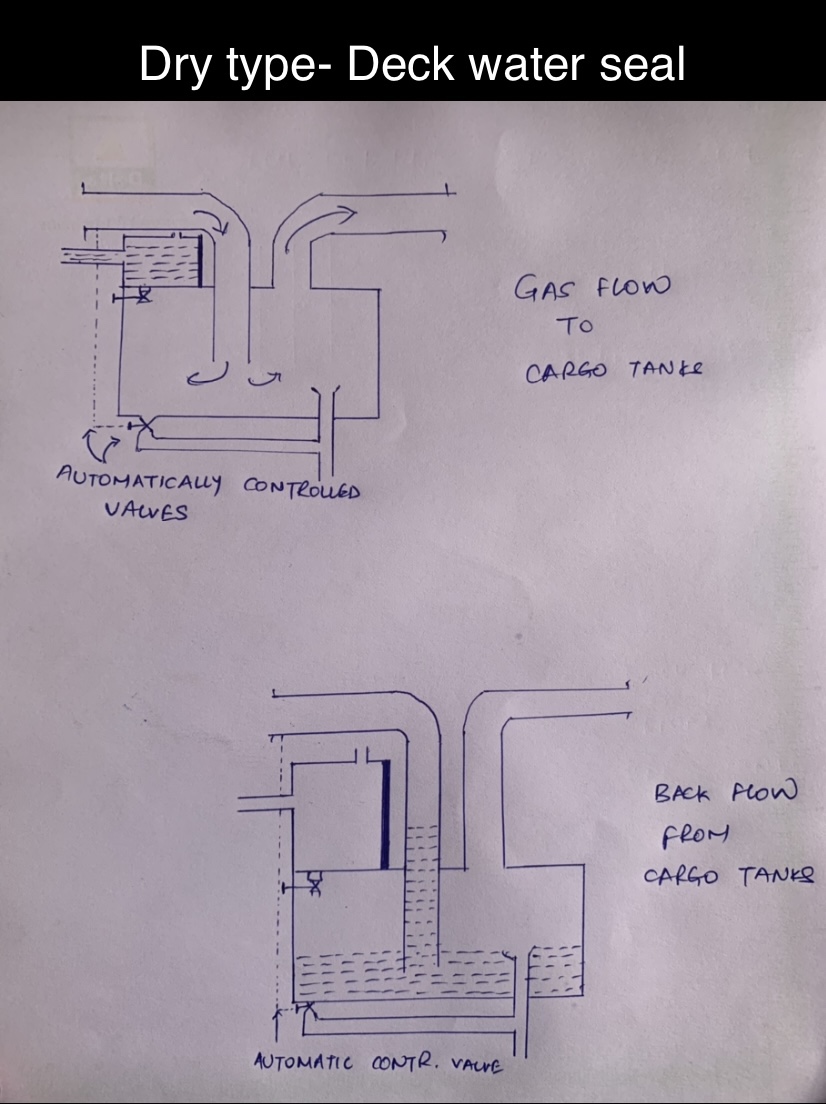
Dry deck seal
PV valves and PV breaker
PV valve: PV valve is a device fitted on individual cargo tank to maintain the tank pressure within prescribed limits.
All cargo tanks have pressure limits, which has to be maintained inside the cargo tanks. ( for example let’s take the limit as +1700 mmwg and -370 mmwg)
The limit includes the maximum pressure and the minimum pressure (vacuum) which the tank can be exposed to.
So till the time tank pressure is within designated limit, it is safe for the structure.
The moment tank gets over pressurised or comes under vaccum, there are chances for tank rupture.
So in order to prevent that, the PV valve activates.
The PV valve releases the excess pressure if the tank is over pressurised. In case of the example taken above, if the pressure reaches above +1700 mmwg, the PV valve lifts up and releases the excess pressure.
While on the other hand it sucks air from outside if the tank gets under-pressurised. Same like above, if it reaches below -370 mmwg, it will suck the air from outside and maintain the pressure limit inside the cargo tank.
PV breaker: PV breaker is fitted on the IG main line.
The purpose is more or less same as PV valve. PV breaker also acts to prevent the over pressurisation or under pressurisation of cargo tanks.
The structure quite a bit different from PV valve.
PV breaker has two concentric tubes or pipes, which is filled with liquid (water and glycol). The inner tube in connected to IG main line.
So when the pressure inside the IG main line or the cargo tanks increases, it reaches to the PV breaker.
The Liquid inside the PV breaker resists the pressure until the set limit.
As soon the pressure inside the line increases the designated pressure limit, it exerts the pressure on the liquid inside the PV breaker.
So the water is thrown out and the PV breaker empties. Thus the over pressure is avoided by emptying out the PV breaker.
While on the opposite side, vaccum inside the IG main line causes the liquid to be sucked inside, and the preventing the rupture or collapsing of IG line and cargo tanks.
Why bunker tanks are not inerted ..??
In second mates or chief mates orals, surveyors have been asking this question since many years.
That bunker tanks also contain diesel, Fuel oil or other fuels containing hydrocarbon.
Then why the IG plant or IG system is used only for cargo tanks and not for bunker tanks.
So let’s get to this.
As you know that we need we need three components to complete a fire triangle.
Which are
– Oxygen
– Heat or any source of heat &
– Fuel (cargo vapours)
So inside the cargo tanks we already have cargo vapours as well as source of heat.
The source of heat is the sparks which may be generated during cargo operation, tank cleaning operation or any other operation causing static electricity.
So we are removing the third component(oxygen) by introducing IG.
When we introduce IG inside the cargo tanks. The oxygen level comes below 8%. So it will lie outside the explosive limit and hence won’t cause any explosion.
While on the other hand, bunkers have flashpoint of more than 60 degree Celsius.
As we know flashpoint is the temperature where the liquid gives off sufficient vapours to support combustion.
While the temperature does not reach above 60 degree Celsius, it does not give sufficient vapours to support combustion.
And on the other hand, there are very little or no chances of static electricity generation inside the bunker tanks.
So there is no need of IG inside the bunker tanks.
Conclusion
As we have discussed, that based on the construction, there are three kinds of deck water seals.
Which are wet type, semi dry type and dry type deck water seals.
We have also seen the difference between PV valve and PV breaker.
While PV valves are set up for individual tanks, the PV breaker is connected to main IG line in order to prevent the IG line and cargo tanks rupture or collapsing.